Project Experience

Each project presents numerous challenges depending on its scope and timeline. Over the years I’ve experienced many projects in various settings such as academic prototyping, industrial prototyping, and industrial production. Some challenges are typical while others are unique, depending on the requirements.
Early in the conceptual and planning phase is where the performance requirements and timeline are established. It’s essential to have clear goals from the start to ensure that a project progresses efficiently. Concept designs will be created and reviewed here, and any calculations / simulations will be performed to support validation.
Once the design has been sufficiently reviewed and accepted, the manufacturing documents will be completed and sent out to be produced. Logging all costs and turnaround times for each part reduces risks for achieving timeline and budget goals.
While parts are waiting to arrive, it’s a good time to work on assembly instructions and testing plans. This way there will be a clear path for how each part should go together correctly. Testing is performed to confirm that performance specifications are met. Final documentation will provide historic insight on areas of improvement to be made in the next revision of the design.
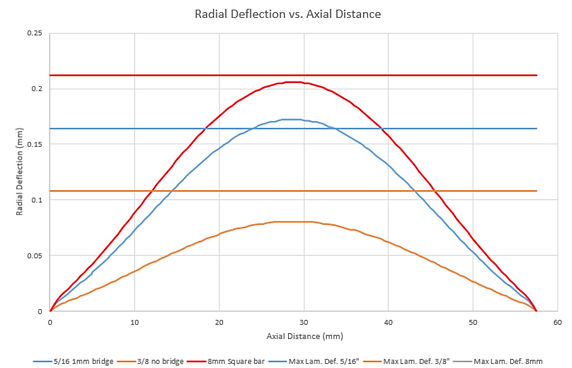
FEA results for a deflection analysis on inner components of magnetic gearbox
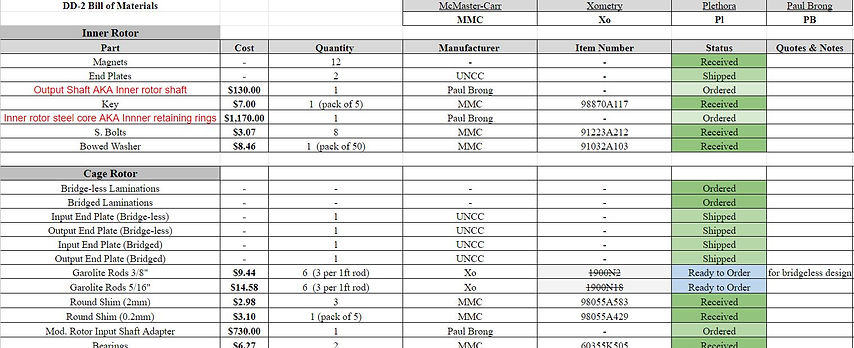
One section of a bill of materials for the DD-2 magnetic gearbox design

Drawing for a part that was made in-house (UNCC machine shop)
DD-2 magnetic gearbox assembly

Oscilloscope reading from a frequency analysis experiment